3D Ink Printing and Sintering of Metals and Alloys
John Misiaszek , *Chun-Te Wu ,and *Dr. Christoph Kenel
3D ink extrusion and co-reduction of pre-alloyed powder, mixed elemental, or oxide or hydride blends
allows to create alloys and intermetallics in situ upon thermal treatment. In case of alloys
interdiffusion is required to homogenize the compositional differences, unless pre-alloyed powder
is used. Such pre-alloyed powder is typically more expensive than elemental powders and limits
compositional flexibility. For many alloy systems, the metallic constituents can be reduced or
decomposed from compounds (such as oxides or hydrides) to access sub-micron powder sizes. In
their metallic form such small powders tend to be oxidized and be difficult to handle, whereas
oxides are fully stable in air. Using small powders greatly accelerates sintering kinetics and
allows to fully densify the printed material.
3D printed titanium alloy scaffolds filled with bioactive slurry for therapeutic bone implants
John Misiaszek
collaborate with Nick Sather in Stupp Lab
Titanium has experienced clinical success as a bone implant material due to its high fracture toughness, excellent corrosion resistance, and favorable biological integration properties. However, titanium has demonstrated drawbacks in implant reliability via stress shielding and poor osseointegration.
Stress shielding is caused by a stiffness mismatch between pure Ti implant (110 GPa) and the surrounding bone (2-25 GPa), causing the implant to take up most of the applied load, promoting bone resorption and implant loosening. The inert nature of titanium reduces the cellular attachment and integration to the implant, detrimentally affecting the reconstruction of the bone and ultimately causing chronic failure. Greater surface roughness, surface area, and surface free energy are metrics associated with greater osseointegration.
In my work, I seek to 3D-extrude titanium-powder inks into structured, lattices with struts displaying microporosity via leachable salt spaceholders to increase osseointegration whilst simultaneously reducing stiffness for the application of intervertebral implants. The ~ 1 mm wide channels within the printed lattice (macroporosity) allows for nutrient transport and vasculature growth; the microporosity within the struts from the salt spaceholder, on the size scale of 50-100 microns, provides a size, roughness, and morphology in which osteoblastic cells will preferentially colonize.
Related publications:
- Sargeant, T. D., Oppenheimer, S. M., Dunand, D. C. & Stupp, S. I. Titanium Foam-Bioactive Nanofiber Hybrids for Bone Regeneration. J. Tissue Eng. Regen. Med. 2, 455-462 (2008).
- Spoerke, E. D. et al. Titanium with aligned, elongated pores for orthopedic tissue engineering applications. J. Biomed. Mater. Res. A 84A, 402-412 (2008).
- Bansiddhi, A. & Dunand, D. C. Shape-memory NiTi foams produced by replication of NaCl space-holders. Acta Biomater. 4, 1996-2007 (2008).
- Ye, B. & Dunand, D. C. Titanium foams produced by solid-state replication of NaCl powders. Mater. Sci. Eng. A 528, 691-697 (2010).
- Bansiddhi, A. & Dunand, D. C. Shape-memory NiTi foams produced by solid-state replication with NaF. Intermetallics 15, 1612-1622 (2007).
- Li, H., Oppenheimer, S. M., Stupp, S. I., Dunand, D. C. & Brinson, L. C. Effects of Pore Morphology and Bone Ingrowth on Mechanical Properties of Microporous Titanium as an Orthopaedic Implant Material. Mater. Trans. 45, 1124-1131 (2004).
- Song, B., Kenel, C. & Dunand, D. C. 3D ink-extrusion printing and sintering of Ti, Ti-TiB and Ti-TiC microlattices. Addit. Manuf. 35, 101412 (2020).
- Kenel, C., Geisendorfer, N. R., Shah, R. N. & Dunand, D. C. Hierarchically-porous metallic scaffolds via 3D extrusion and reduction of oxide particle inks with salt space-holders. Addit. Manuf. 37, 101637 (2021).
Funding support
- NSF GRFP, 2021-2024
- GEM Fellowship, 2024-2024
Affordable Low Modulus Titanium Alloys
Chun-Te Wu and Dr. Christoph Kenel
New project; description coming soon!
High entropy alloy microlattices
Ya Chu Hsu, Dingchang Zhang and Dr. Christoph Kenel
Here, the used ink contains a blend of Co3O4+Cr2O3+Fe2O3+NiO that is reduced to metallic Co, Fe, Ni that interdiffuse and accept freshly reduced Cr to form an equiatomic CoCrFeNi high entropy alloy. This approach allows to create a wide range of (non-)equiatomic compositions without limitations on powder availability. Additionally, using fine oxide powders leads to small metal grains that further accelerate sintering. The resulting high entropy alloy microlattices have dense struts, but a controlled level of macroporosity, defined by their strut assembly. This allows to control the mechanical properties of the microlattice. Based on the good ductility of CoCrFeNi, the microlattices show excellent behavior at ambient and cryogenic temperatures.
Here, we successfully demonstrate that CoCrCuFeNi high-entropy alloy microlattices can be fabricated by extrusion printing of ink containing a blend of oxides (Co3O4, CuO,Fe2O3, and NiO) and metal powder (Cr) followed by co-reduction in hydrogen and sintering. This method avoids the problems of residual stress and textured microstructure that occur in laser/electron-based additive manufacturing methods and offers flexibility in using metal compounds (rather than pyrophoric metals) and submicron powders (accelerating sintering). This research focuses on understanding the co-reduction of oxides by in-situ X-ray diffraction, studying microstructural evolution after solid and liquid sintering, and explaining compressive properties of CoCrCuFeNi microlattices by Finite Element Modeling.
We are also investigating this method for refractory high-entropy alloys with bcc crystal structure
Related publications:
- C. Kenel, N.P.M. Casati, D.C. Dunand, 3D ink-extrusion additive manufacturing of CoCrFeNi high-entropy alloy microlattices, Nature Communications 10 (2019) 904.
- D.C. Zhang, C. Kenel, D.C. Dunand, Microstructure and mechanical properties of 3D ink-extruded CoCrCuFeNi microlattices, Submitted.
Funding support
- Swiss National Science Foundation, Early Postdoc Mobility fellowship 2017-2018 under grant No. 172180
- NSF Funding project (NSF DMR-2004769)
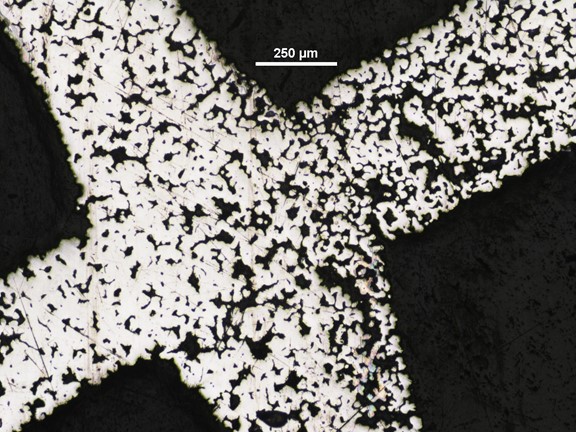
Optical micrographs of extruded Ti+NaCl ink, at a lattice junction, after sintering. High porosity in the Ti struts is caused by the NaCl spaceholders, partial sintering of Ti powders, and air bubbles
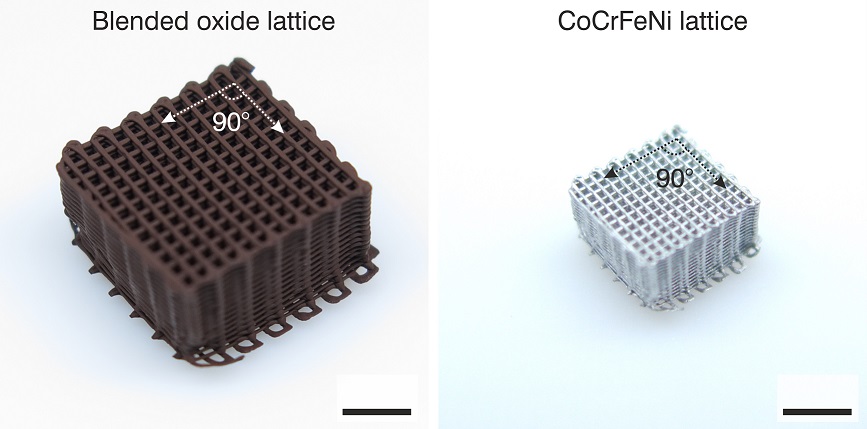
Microlattice 3D ink extruded from Co3O4+Cr2O3+Fe2O3+NiO loaded ink (left). After co-reduction and sintering in H2 a fcc CoCrFeNi high entropy alloy microlattice is formed (right). Scale bar: 3 mm.
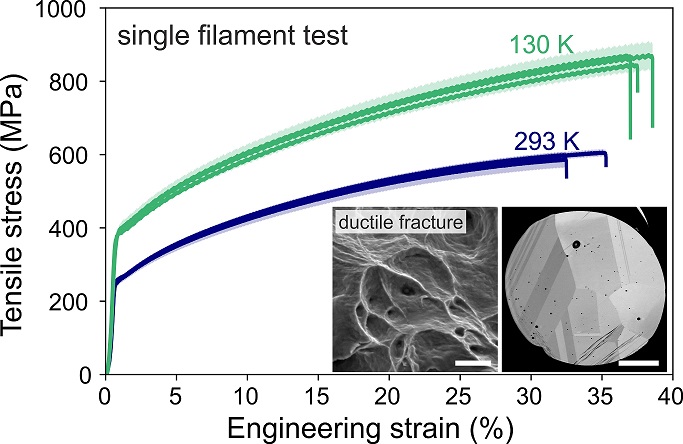
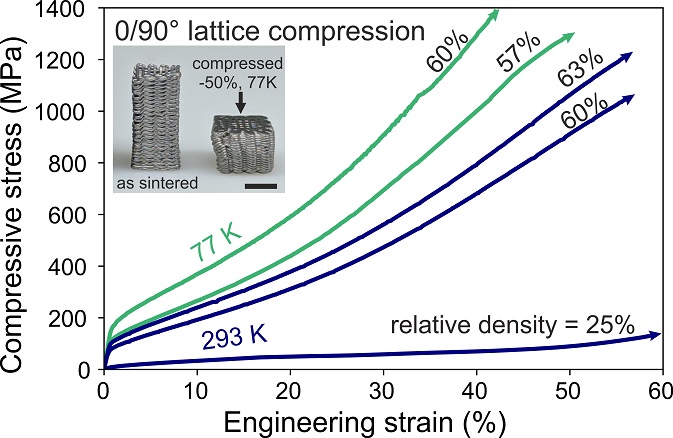
The 3D ink extruded and sintered CoCrFeNi single filaments and microlattices show excellent mechanical behavior at ambient and cryogenic temperatures.
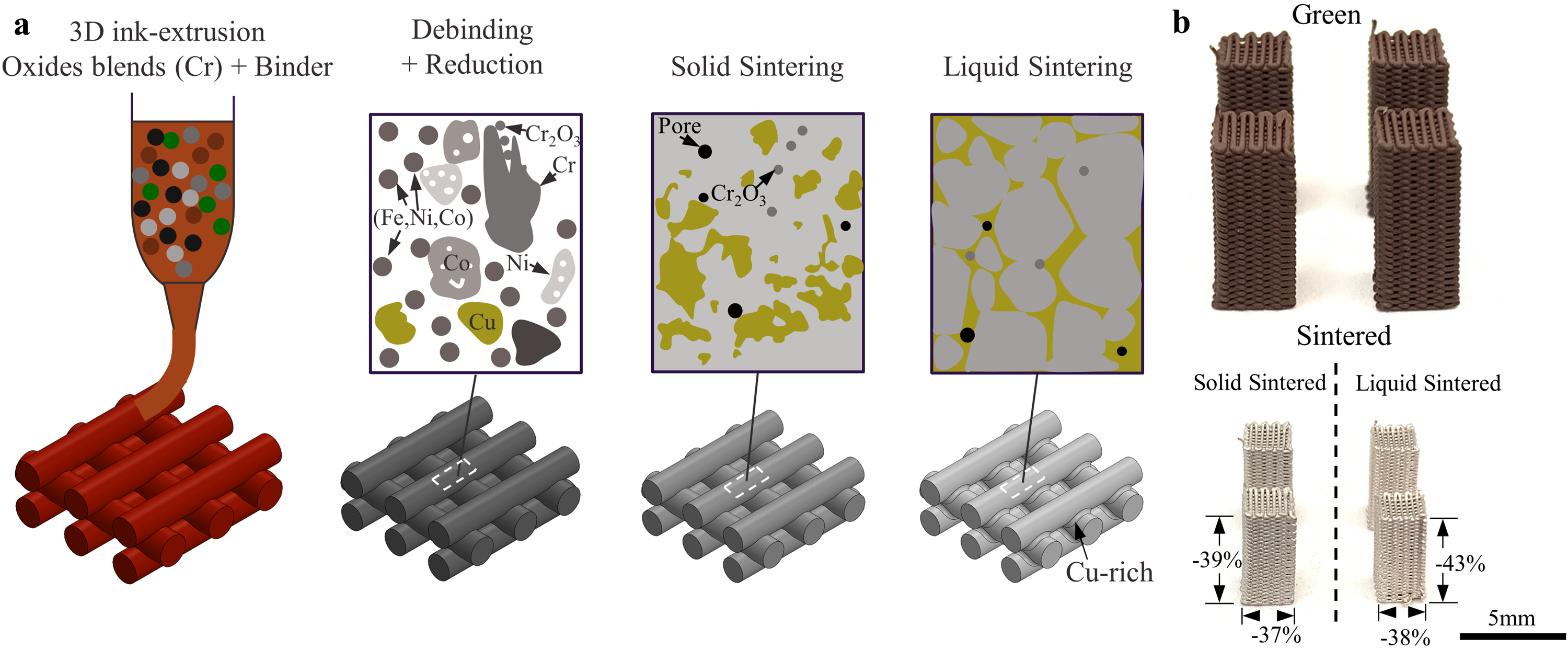
(a) Schematic of 3D ink extrusion, reduction, and sintering process; (b) photographs of CoCrCuFeNi microlattices printed from Co3O4-Cr-Fe2O3-NiO-CuO inks, (left) after solid sintering (1050 ?C / 4 h ) and (right) after liquid sintering (1050-1150 ?C / 4 h).