3D Ink Printing and Sintering of Ceramics and Composites
Dingchang Zhang, Dr. Christoph Kenel, *Pengyu Chen, *Prof. Binna Song, *Jens Sesseg, and *Micha Calvo
3D ink extrusion followed by sintering is capable of creating complex metallic and ceramic structures. Brittle ceramics/semiconductors can be printed and sintered similar to metals allowing complex structures to be additively manufactured. 3D printed structures can be further converted into composites by infiltration with liquid metal into metallic and ceramic lattices (W-Cu, Ag-SnO2) or directly be printed by using ink that contains metallic and ceramic particles (WC-Co, Ti-MMC) that are then sintered together.
The infiltration approach typically yields a fully dense composite with the infiltration liquid filling all open porosity in the 3D printed material thus creating an interpenetrating network of both phases. Changing 3D printing parameters allows then to change the morphology and fraction of the reinforcement phase.
Printing of inks containing both metallic and ceramic particles that form a composite after sintering, allows to create a complex structure, where each lattice strut is a composite strut itself. The space in between filaments can remain open to create composite lattices.
3D printing of silicon for battery applications
Simon Moser and Dr. Christoph Kenel
Current graphite anodes in Li-ion batteries have a capacity of 372 mAh g-1 whereas silicon has a theoretical capacity 10x higher. In spite of this immense advantage, bulk silicon is not used as anode due to its large volumetric change during (de)lithiation (up to 300%) leading to internal stresses and pulverization after only a few cycles. Here, we explore additively- manufactured architectures for sintered Si which can withstand these internal stresses.
Additive manufacturing of metals is usually done via selective laser melting (SLM) or selective laser sintering (SLS). However, SLM is very difficult for silicon given its high thermal conductivity, high reflectivity and a high tendency to form oxides, while SLS is unattractive because of silicon's slow sintering kinetics. Therefore, we use an extrusion-based method (direct ink writing) to create Si anode with porous architectures, and we investigate both steps of ink printing of Si powders and their subsequent sintering.
Related Publications
-
Calvo M, Jakus AE, Shah RN, Spolenak R, Dunand DC. Microstructure and Processing of 3D Printed Tungsten Microlattices and Infiltrated W-Cu Composites. Advanced Engineering Materials. 2018;20(9):1800354.
-
Reyes Tirado FL, Huang J, Dunand DC. Ice-templated silicon foams with aligned lamellar channels. MRS Communications. 2017;7(4):928-32.
Funding support
- Laboratory of Nanometallurgy (ETH Zurich)
Complex WC-Co, WC-Cu, and ZrC-W architectures
Dingchang Zhang and
Dr. Christoph Kenel;
Collaborators on ZrC-W research: Mario Caccia, Kenneth H. Sandhage (Purdue University)
- Laboratory of Nanometallurgy (ETH Zurich)
Complex WC-Co, WC-Cu, and ZrC-W architectures
Dingchang Zhang and Dr. Christoph Kenel; Collaborators on ZrC-W research: Mario Caccia, Kenneth H. Sandhage (Purdue University)
WC-Co is the most widely used cemented carbide in industry thanks to its high hardness, modulus and wear resistance combined with a good fracture toughness. WC/Co parts are conventionally produced using powder metallurgy and sintering, that is inherently limited by the complexity of the resulting parts. Additionally, WC/Co is difficult to produce using beam-based AM due to high residual stresses and cracking. Here, 3D ink printing of WC+Co containing ink followed by sintering is used to create complex WC/Co architectures. A tight control of composition and sintering conditions allows to tailor the resulting grain size and mechanical properties.
Zirconium carbide (ZrC) and tungsten (W) are refractory materials with some of the highest melting temperatures and Young's moduli. Co-continuous ZrC/W composites combine attractive characteristics of ZrC with those of W. These composites are also thermally- and chemically-compatible, as ZrC and W exhibit similar thermal expansion coefficients. Such attractive mechanical behavior, along with high thermal conductivity and resistance to both thermal shock and erosion make ZrC/W composites well suited for critical components used in applications under extreme thermal and mechanical conditions. We demonstrate that 3D ink extrusion printing may be coupled with the Displacive Compensation of Porosity (DCP) process to yield finely-featured, complex-shaped, ultra-high-melting, co-continuous ZrC/W structures.
Related Publications
-
Zhang D, Kenel C, Dunand DC. Microstructure and properties of additively-manufactured WC-Co microlattices and WC-Cu composites. Acta Materialia. 2021 Dec 1;221:117420.
-
Zhang D, Kenel C, Caccia M, Sandhage KH, Dunand DC. Complex-shaped, finely-featured ZrC/W composites via shape-preserving reactive melt infiltration of porous WC structures fabricated by 3D ink extrusion. Additive Manufacturing Letters. 2021 Dec 1;1:100018.
3D ink printing of Ti-MMC lattices
*Prof. Binna Song and
Dr. Christoph Kenel
Ti and its composites find widespread application in biomedical and aerospace industries because of their biocompatibility, strength and wear resistance combined with a low density. Here, 3D ink printing is used to create Ti-based MMC lattice structures by co-printing Ti and ceramic particles. The lattices are then sintered in vacuum to densify the composite struts. In order to conserve the delicate lattice structure, only pressure-less sintering can be applied.
This study focuses on creating Ti-MMCs with reinforcement levels above the percolation threshold, requiring rapid densification kinetics.
Funding support
- China Scholarship Council
Additive manufacturing of Ag-SnO2 contact materials
*Pengyu Chen, and Dr. Christoph Kenel
SnO2-Ag composites are widely used as contact materials in low-voltage instruments. Commercial composites are made by powder sintering and show a random network of the SnO2 and Ag phases. The composite architecture greatly affect arc erosion behaviour, contact resistance, and anti-welding ability. Here, we use extrusion 3D-printing to fabricate, and then sinter, regular 0/90° SnO2 scaffolds whose open porosity is then melt-infiltrated with silver. The regular SnO2 phase architecture in the composite is expected to improve arc erosion resistance because the SnO2 scaffold will impede the flow and splashing of molten silver during arcing. Meanwhile, the continuous silver matrix channels conducts current effectively, and is expected to achieve a lower contact resistance than commercial products where Ag shows a tortuous morphology. We study here the densification mechanism of the SnO2 scaffolds during sintering, the infiltration behaviour of liquid silver, and the properties of the composites.
Additive manufacturing of tungsten by reduction and sintering
*Jens Sesseg, Dr. Christoph Kenel, and *Micha Calvo
in collaboration with Prof. Spolenak (ETH Zurich)
Tungsten micro-lattices, with 0/90° strut structures or more complex gyroid architectures, are produced by direct ink writing of a slurry of WO3-0.5% NiO submicron powders, followed by H2 reduction and Ni-activated sintering. The green bodies undergo isotropic linear shrinkage of ~50% during the thermal treatments resulting in microlattices, with overall ~50% open porosity, consisting 95-100% dense tungsten struts ~100 μm in diameter. Ball-milling of the powders and inks reduces the sintering temperature needed to achieve full densification from 1400 to 1200 °C and enables the ink to be extruded through a 200 µm nozzle. Full sintering densification is achieved through the addition of 0.5 wt% NiO to the slurry, which was also beneficial for the following infiltration with liquid copper. Partially-sintered struts with submicron open porosity were also infiltrated with Cu, resulting in a co-continuous W/Cu composites with wide W struts/Cu channel at the lattice scale, and fine W/Cu interpenetrating skeletons at the strut scale.
Related publications:
- Calvo M, Jakus AE, Shah RN, Spolenak R, Dunand DC. Microstructure and Processing of 3D Printed Tungsten Microlattices and Infiltrated W-Cu Composites. Advanced Engineering Materials. 2018;20(9):1800354.
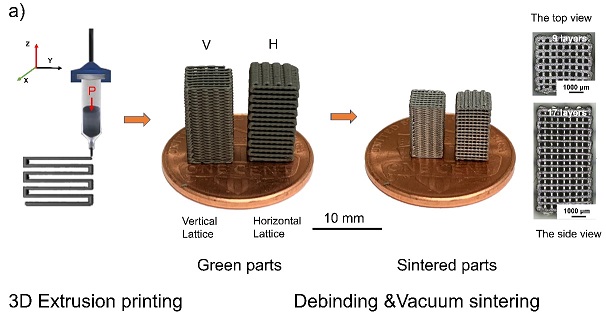
Fig. 1. 3D printing of Ti+ceramic ink followed by vacuum sintering to create Ti-MMC lattices
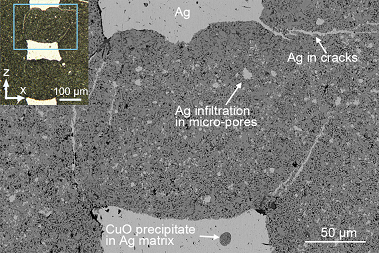
Microstructure of SnO2-Ag composite produced by pressure-less Ag infiltration of a SnO2 micro-lattice. Ag additionally infiltrates into cracks at filaments joints and remaining micro-pores inside the filaments.
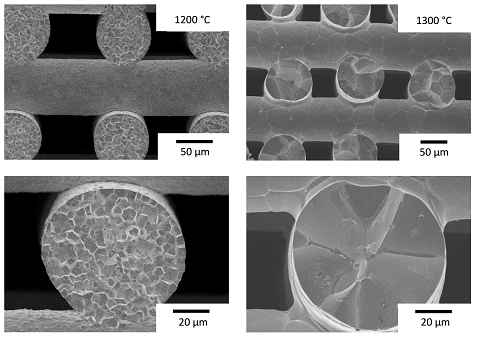
Fig. 2. SEM images of sintered metallic W struts in 0/90° scaffolds produced via extrusion of ball-milled WO3-0.5% NiO inks, followed by reduction and sintering for 1 h at 1200 °C (left) and 1300 °C (right). Struts are fully densified and grain size is strongly reduced when lowering the sintering temperature from 1300 °C (20 - 50 μm) to 1200 °C (5 - 10 μm).
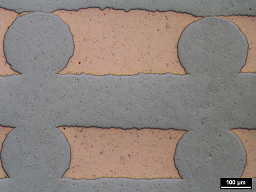
Fig. 3. Optical micrograph of a polished cross-section of a W-Cu composite produced by Cu infiltration of W scaffolds.
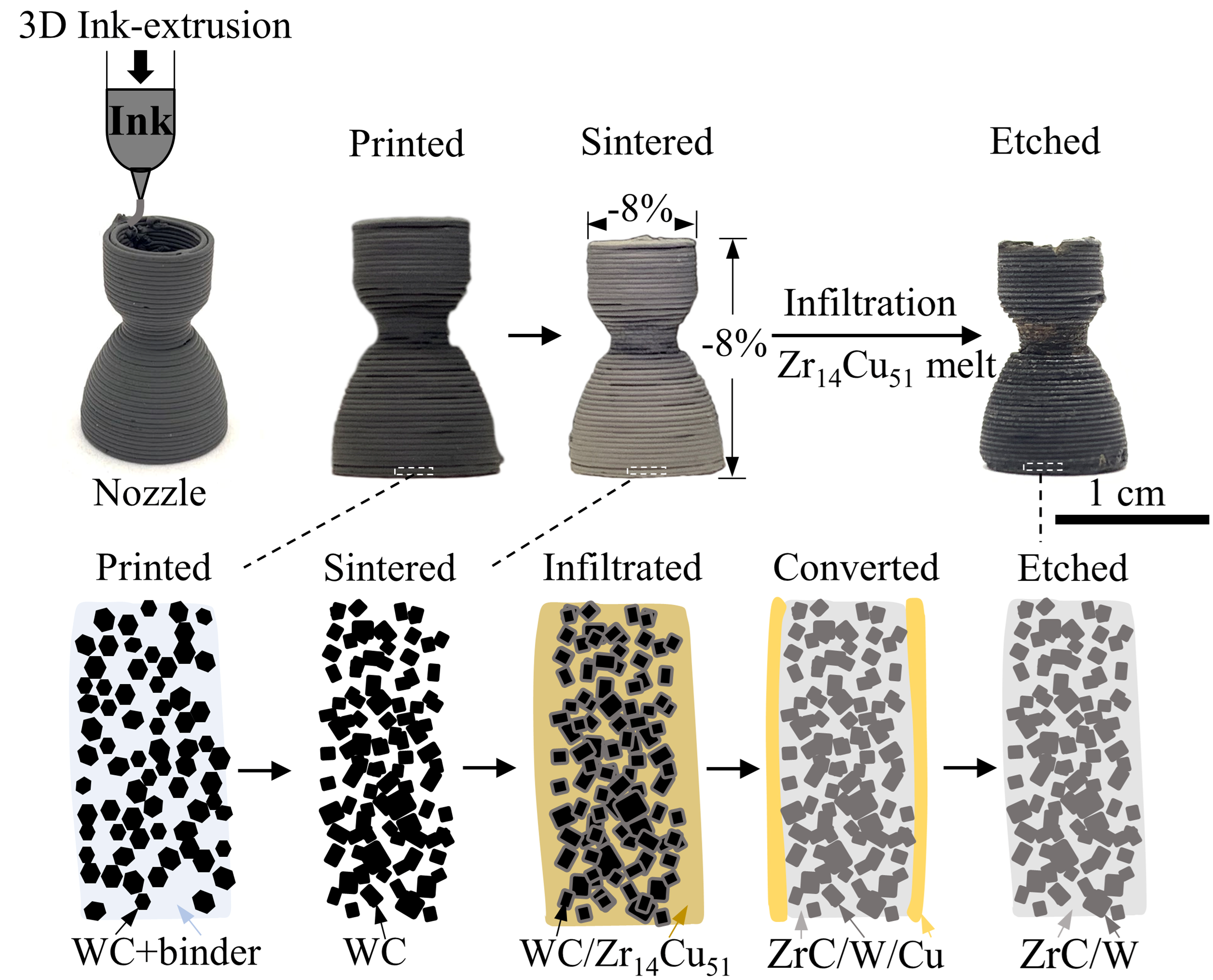
Fig. 4. Top row: Photographs of the centimeter-scale nozzle after 3D printing (WC + binder), after partial sintering (porous WC; 1650 °C / 1 h) and after conversion/etching (ZrC/W, peak reaction temperature of 1350 °C for 1 h) at the same magnification, showing shrinkage values. Bottom row: Schematic illustration of the microstructural evolution at various processing stages.