Hierarchically strengthened aluminum-based superalloys
Clement Ekaputra,Ismael E. Coello,Logan White and Dr. Jovid Rakhmonov;
co-advised by Dr. Jon-Erik Mogonye, U.S. Army Development Command Army Research Laboratory
Aluminum alloys are desirable for many energy applications; in particular in applications such as the aerospace industry where high strength, lightweight, and corrosion-resistant materials are desired. While aluminum alloys have already been in wide use for low-temperature applications, there is interest in extending the applications of aluminum alloys to elevated-temperature applications (>300C). However, many commercial aluminum alloys lose their strength rapidly at elevated temperatures, due to coarsening of strengthening precipitates. As a result, there is interest in developing aluminum alloys strengthened by phases that resist coarsening at elevated temperatures.
There has been a wide body of research looking into such coarsening-resistant alloy systems, such as the Al-Ce or Al-Ni systems strengthened by a high volume fraction of intermetallics formed during solidification, L12-Al3(Sc,Zr) or α-Al(Mn)Si precipitates formed during aging, or slow-diffusing solutes such as Mn which provide high solid-solution strengthening at elevated temperatures. Research focuses on experimentally probing the microstructure and mechanical behavior of these strengthening phases individually, as well as combining these strengthening phases or adding other elements to improve them further. A variety of microstructural characterization techniques are used at multiple length scales to develop a comprehensive understanding of the alloys developed here, such as scanning and transmission electron microscopy, and atom-probe tomography.
The effect of processing technique is also emphasized, as many of these alloys were originally developed for traditional casting techniques. We focus now on laser powder-bed fusion additive manufacturing, a technique by which complex geometries can be built layer-by-layer by scanning a powder bed with a laser to melt selected regions. Another benefit is high solidification rates inherent to the process, which greatly refines the resulting microstructure compared to conventionally cast alloys, further unlocking new potential for alloy exploration.
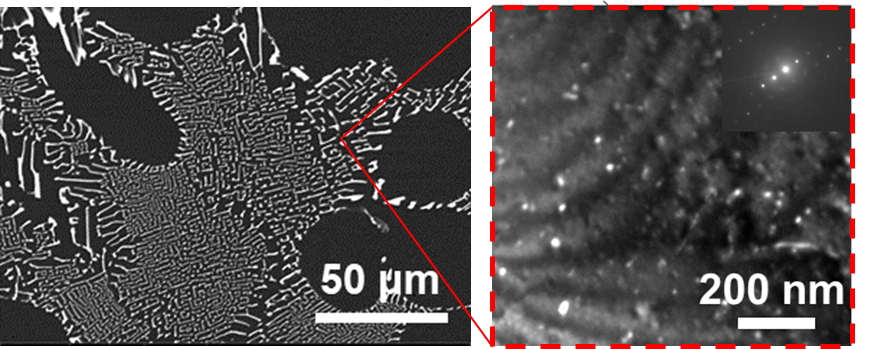
A number of aluminum alloy systems feature coarsening-resistant precipitates, such as the Al-Ce, Al-Sc-Zr, and Al-Mn-Mo-Si systems. The aim of this study is to investigate the effects of combining these elements into a single alloy system, and design alloys for casting and selective laser melting with excellent high-temperature mechanical performance.
Related Publications
- Jovid U. Rakhmonov, Nhon Q. Vo, Joseph R. Croteau, Joshua Dorn, David C. Dunand, Laser-melted Al-3.6Mn-2.0Fe-1.8Si-0.9Zr (wt%) alloy with outstanding creep resistance via formation of ?-Al(FeMn)Si precipitates, Additive Manufacturing, Volume 60, Part B, 2022, 103285, ISSN 2214-8604, https://doi.org/10.1016/j.addma.2022.103285.
- Jovid U. Rakhmonov, David Weiss, David C. Dunand, Solidification microstructure, aging evolution and creep resistance of laser powder-bed fused Al-7Ce-8Mg (wt%), Additive Manufacturing, Volume 55, 2022, 102862, ISSN 2214-8604, https://doi.org/10.1016/j.addma.2022.102862.
- Clement N. Ekaputra, Jovid U. Rakhmonov, David Weiss, Jon-Erik Mogonye, David C. Dunand, Microstructure and mechanical properties of cast Al-Ce-Sc-Zr-(Er) alloys strengthened by Al11Ce3 micro-platelets and L12-Al3(Sc,Zr,Er) nano-precipitates, Acta Materialia, Volume 240, 2022, 118354, ISSN 1359-6454, https://doi.org/10.1016/j.actamat.2022.118354.
- Clement N. Ekaputra, David Weiss, Jon-Erik Mogonye, David C. Dunand, Eutectic, precipitation-strengthened alloy via laser fusion of blends of Al-7Ce-10Mg (wt.%), Zr, and Sc powders, Acta Materialia, Volume 246, 2023, 118676, ISSN 1359-6454, https://doi.org/10.1016/j.actamat.2023.118676.
Funding support
- U.S. Army Development Command Army Research Laboratory