Aluminum Alloys
Dr. Amir R. Farkoosh, Dan Rosenthal, *Dr. Shipeng Shu, *Dr. Dinc Erdeniz, *Dr. Anthony De Luca, *Dr. Jacques Perrin Toinin, *Dr. Richard Michi, and *Chanun Suwanpreecha
*researcher graduated/completed assignment
High-Temperature Aluminum Alloys
There are many practical examples where materials are required to survive for long periods under load at high temperatures - a classic example is in the turbine blades of jet engines. In the interest of improved efficiency and performance it is desirable to maximize the operating temperatures while minimizing overall weight. An aluminum alloy with high temperature capability, therefore, is an attractive alternative to the titanium-based components currently used in the frontal sections of jet engines.
Based on the behavior of nickel-base superalloys, which resist degradation of mechanical properties to approximately 75% of their absolute melting temperature, it is conceivable that aluminum-based alloys could be similarly developed which would be useful to 400 °C. As is true for γ' in the nickel-base systems, a high-temperature aluminum alloy must contain a suitable dispersed phase, which must be thermodynamically stable at the intended service temperature.
The creep resistance of nickel-base superalloys is achieved by the presence of ordered Ni3(Al,Ti) precipitates. These precipitates, usually termed γ', have the cubic L12 structure and are therefore isomorphous with the fcc Ni-alloy matrix (called the γ phase). The low mismatch in the lattice parameter between the γ matrix and the γ' precipitates confer particle stabilities well beyond the levels possible with precipitates having a high particle/matrix interfacial energy, and hence these stable precipitates are effective barriers to dislocations at elevated temperatures.
An effective high temperature aluminum alloy should exhibit a similar structural constitution. Trialuminide intermetallic compounds (Al3X) have many attractive characteristics, such as low density, high specific strength, good heat resistance and excellent oxidation resistance. Therefore, they are excellent candidates for use as dispersoids or precipitates in the design of high strength Al alloys for high temperature applications. We investigate microstructure, strength, and creep properties of Al-Sc alloys with rare earth (RE), Zr, and Li additions.
Precipitation-strengthened Al-Sc alloys with Li and Yb additions
Al-Sc alloys have been demonstrated to exhibit high strength at ambient temperature due to the formation of L12-ordered Al3Sc precipitates. On an atom-per-atom basis, Sc is the most potent strengthening addition to Al alloys. Additions of Li, the lightest of all metals, to Al result in an increase in strength due to both solid solution strengthening and the formation of the L12-ordered d'-Al3Li phase, which can have high volume fractions of up to 30%, whereas the low solubility of Sc in Al limits the volume fraction of Al3Sc to only about 1%. Additions of rare earth elements, including Yb, to Al-Sc results in the formation of core/shell Al3Yb/Al3Sc precipitates, with increased lattice parameter mismatch compared to single-phase Al3Sc, with a resultant improvement in creep resistance.
Current research by Matt involves measuring the effects of Li and Yb additions to Al-Sc alloys. While the ambient temperature strength improves with Li addition due to a resultant increase in the volume fraction of Al3(LixSc1-x) precipitates, the creep behavior suffers, because the lattice parameter mismatch is reduced. If both Li and Yb additions are made, the creep resistance of the alloy is restored, since the effects of those elements on the lattice parameter are offsetting.
When a two-step aging treatment is used for Al-Li-Sc-Yb alloys, core/double-shell precipitates are formed (FIGURE 1), with Yb and Li segregated to the Al3(Li+Yb) core, Sc and Li segregated in a first Al3(Li+Sc) shell, and Li segregated in a second Al3Li shell. These complex precipitates confer high-strength to the aged alloy.
Microstructural measurements of the precipitates are measured by TEM and Local Electrode Atom Probe (LEAP) tomography. These measurements are used to inform models that describe the ambient and elevated- temperature behavior of the alloys. In addition to widely-used closed-form solutions, we also employ dislocation dynamics simulations (FIGURE 2). With these, we are able to model the strength of alloys strengthened by complex precipitates, such as those produced during double aging of Al-Li-Sc-Yb.
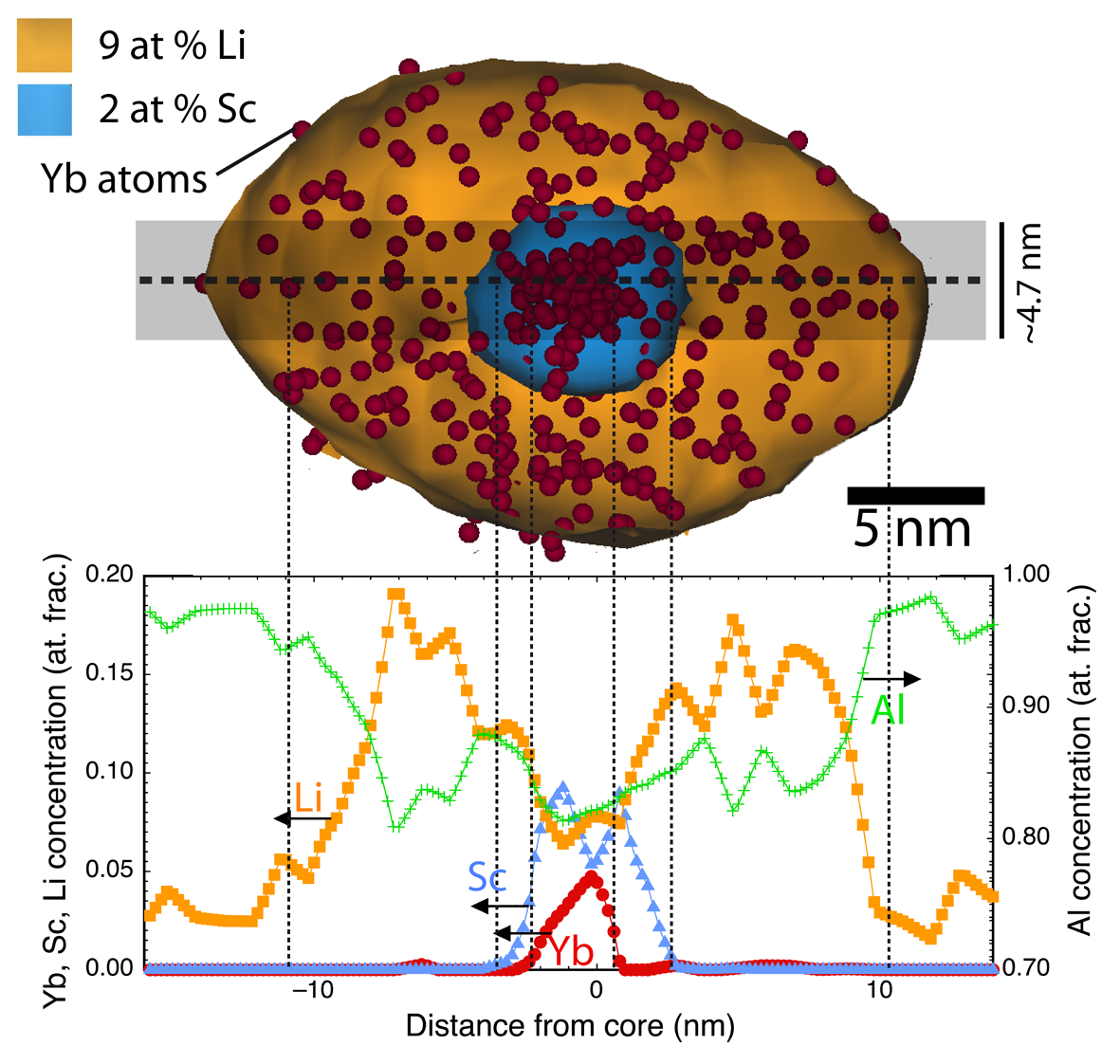
FIGURE 1: A core/double-shell precipitate imaged using the LEAP, after aging for 8 h at 325 °C followed by 2 weeks at 170 °C. The core/double shell structure is evident.
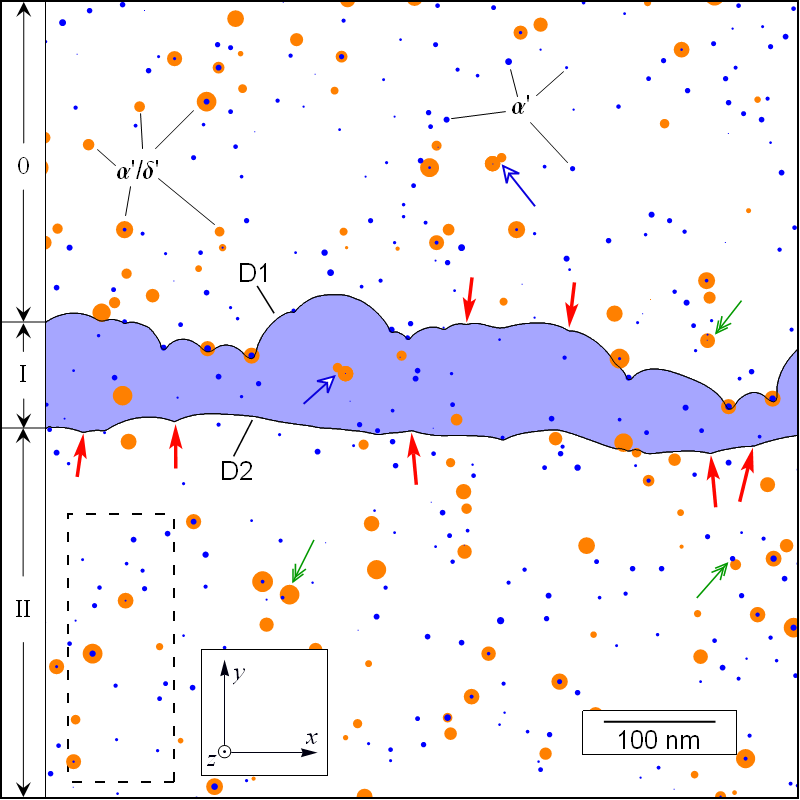
FIGURE 2: A simulated glide plane, used to predict the strength of an alloy containing core/shell precipitates. The cores are Al3(Li+Sc+Yb), the shells are Al3Li. D1 and D2 are a pair of superdislocations, whose behavior controls the alloy strength.
Funding support
- DOE Office of Basic Energy Sciences
- Qatar National Research Fund, NPRP 7-756-2-284
Related Publications
- Erdeniz, D., Nasim, W., Malik, J., Yost, A. R., Park, S., De Luca, A., ... & Dunand, D. C. (2017). Effect of vanadium micro-alloying on the microstructural evolution and creep behavior of Al-Er-Sc-Zr-Si alloys. Acta Materialia, 124, 501-512
- Marquis EA, Seidman DN, Dunand DC. Acta Mater 2003;51:285.
- Seidman DN, Marquis EA, Dunand DC. Acta Mater 2002;50:4021.
- Karnesky RA, Seidman DN, Dunand DC. Materials Science Forum 2006;519-521:1035.
- Van Dalen, M. E., Dunand, D. C., & Seidman, D. N. (2011). Microstructural evolution and creep properties of precipitation-strengthened Al–0.06 Sc–0.02 Gd and Al–0.06 Sc–0.02 Yb (at.%) alloys. Acta Materialia, 59(13), 5224-5237.
- van Dalen, M. E., Gyger, T., Dunand, D. C., & Seidman, D. N. (2011). Effects of Yb and Zr microalloying additions on the microstructure and mechanical properties of dilute Al–Sc alloys. Acta Materialia, 59(20), 7615-7626.
- Krug ME, Dunand DC, Seidman DN. Acta Materialia 2011;59:1700.