Micro-architectured Ni-based Superalloys
Dr. Dinc Erdeniz
Periodic cellular metals share desirable properties with stochastic metal foams such as low density, and high specific strength, stiffness, sound absorption, damping, and surface area. Furthermore, periodic cellular metals can be micro-architectured to optimize various properties in an isotropic or anisotropic manner, which cannot be achieved with porous or foamed metals due to their irregular structures. Fabrication of such periodic structures from high temperature alloys is highly desirable: for instance, cellular Ni-based superalloys could reduce the mass of jet engine parts while enabling efficient cooling which may enable increased operating temperature of the engine. One particular method is to use superalloy wires to weave or braid structural parts, however there are three significant manufacturing difficulties: (i) commercial superalloy wires are difficult to draw due to their limited ductility and are thus not widely available, especially below ~500 µm diameter; (ii) when available, these superalloy wires are not sufficiently ductile at room temperature to withstand the necessary bending angles for weaving; (iii) bonding of 3D woven superalloy wires is challenging.
In this research, we take a novel approach to overcome these issues by reshuffling the established sequence of the manufacturing steps of (i) alloy casting, (ii) wire drawing, (iii) wire weaving/braiding and (iv) wire bonding. Specifically, we use ductile Ni-20 wt.% Cr precursor wires to weave or braid complex structures and subsequently alloy them by pack cementation (a chemical vapor deposition process), followed by homogenization and aging to achieve superalloy microstructures with γ' precipitates, while also creating bonds at wire contact points. The Ni-20Cr woven part to be alloyed is buried in a powder mixture (the pack) consisting of a filler (usually Al2O3), an activator (a halide salt), and a metal source (pure or in alloy form). At elevated temperature, the activator decomposes and reacts with the source to create a metal halide gas, which subsequently deposits the metal on the substrate surface. The deposited metal diffuses into the substrate and forms a coating, which usually extends a few tenths of millimeters into the part. With this technique we alloy Ni-Cr woven structures with Al, Ti, and Mo, and achieve superalloy microstructure after homogenization and aging.
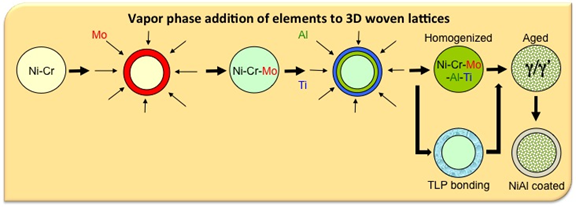
Figure 1: Schematic showing the alloy processing sequence.
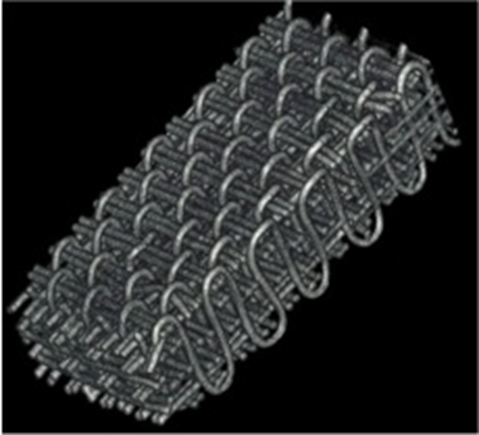
Figure 2: A tomographic image showing the as-woven Ni-Cr structures (image courtesy Andrew Geltmacher and Richard Fonda, NRL, Washington DC).
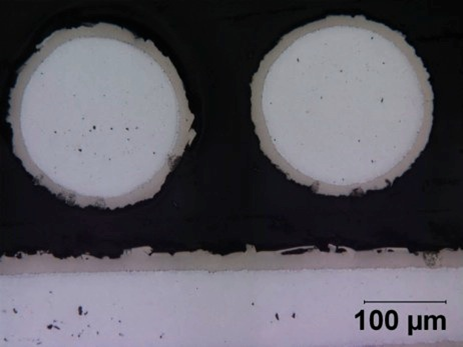
Figure 3: Pack-aluminized Ni-Cr wires with NiAl coatings
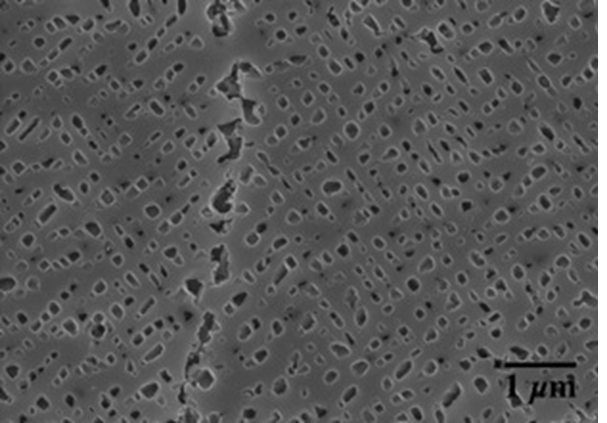
Figure 4: γ/γ' microstructure formed in a Ni-Cr-Al wire after homogenizing and aging.
Funding support
- Defense Advanced Research Projects Agency under award number W91CRB1010004 (Dr. Judah Goldwasser, program manager)
Related Publications
- Erdeniz, D., Schaedler, T. A., & Dunand, D. C. (2017). Deposition-based synthesis of nickel-based superalloy microlattices. Scripta Materialia, 138, 28-31.
- D. Erdeniz, K.W. Sharp, D.C. Dunand, “Transient Liquid-Phase Bonded Ni-Based Woven Superalloys,” Scripta Materialia 108 (2015) 60-63
- D. Erdeniz, A.J. Levinson, K.W. Sharp, D.J. Rowenhorst, R.W. Fonda, D.C. Dunand, “Pack Aluminization Synthesis of Superalloy 3D Woven and 3D Braided Structures,” Metallurgical and Materials Transactions A 46A (2015) 426-438
- Wang, C., & Dunand, D. C. (2015b). Nanoscale Cellular Structures at Phase Boundaries of Ni-Cr-Al-Ti and Ni-Cr-Mo-Al-Ti Superalloys. Metallurgical and Materials Transactions a-Physical Metallurgy and Materials Science, 46A(6), 2680-2687
- Wang, C., & Dunand, D. C. (2015a). Microstructure Evolution During Al, Ti, and Mo Surface Deposition and Volume Diffusion in Ni-20Cr Wires and Woven Structures. Metallurgical and Materials Transactions a-Physical Metallurgy and Materials Science, 46A(5), 2249-2254
- Philippe, T., Erdeniz, D., Dunand, D. C., & Voorhees, P. W. (2015). A phase-field study of the aluminizing of nickel. Philosophical Magazine, 95(9), 935-947
- Erdeniz, D., & Dunand, D. C. (2014). Microstructure development during pack aluminization of nickel and nickel-chromium wires. Intermetallics, 50, 43-53