Gravitationally-driven defects during directional solidification of ice-templated TiO2
Kristen Scotti, Pierce Pettit, *Emily Northard, *Amelia Plunk, *Lauren Kearney, *Jared Burns, and *Matthew Ocana
*researcher graduated/completed assignment
Ice-templating (or freeze-casting with water) is a directional solidification technique that produces materials with highly anisotropic pore structures. The three-step process, consisting of solidification, sublimation, and sintering, is depicted in Fig. 1. Solidification is arguably the most critical step in the process, as the pore morphology of the final product is largely governed by the operational conditions during this stage.
A major advantage of the ice-templating technique is that it inherently allows for the adjustment of microstructural properties through the manipulation of solidification conditions. This is significant because it means that mechanical and physical properties of final products may be tailored to suit desired applications simply by modifying the conditions of solidification, e.g. solidification temperature, solid content of the suspension, particle size, just to name a few. Of course, there are some limitations, but in principle, since the ice dendrites serve as templates for pores in the final product, learning how to precisely control their growth is paramount to achieving a desired final structure.
We are using aqueous suspensions of titanium dioxide as a model suspension system to study the effect of gravity on microstructures templated during directional solidification of ice-templated materials. We previously conducted experiments on reduced gravity parabolic flights and investigated the effect of solidification direction under normal terrestrial gravity; currently, we are investigating the effect of water's density inversion at 4 °C on TiO2 microstructures.
*Microgravity, Parabolic Flight Work
Kristen Scotti, *Emily Northard, and *Amelia Plunk
Initial microgravity investigations of the freeze-casting technique were conducted with NASA's Flight Opportunities Program. Aqueous suspensions of 10-30 nm TiO2 were solidified on parabolic flights in 2014 and 2015 under micro-, lunar (~0.17 g; gl = 1.62 m/s2), and Martian (~0.38 g; gm = 3.71 m/s2) gravity and compared to terrestrially-solidified samples (Fig. 2). Periodic ice lens structures, commonly observed and reported as "ice lens defects" in the ice-templating literature, were observed in titanium dioxide structures that were solidified under normal terrestrial gravity, but these defects were not observed when samples were solidified under reduced gravity conditions. Microstructural tilting away from the applied temperature gradient was observed to increase as gravitational accelerations increased (Fig. 2).
*Effect of Solidification Direction
Kristen Scotti, *Lauren Kearney, *Jared Burns, and *Matthew Ocana
Most directional ice-templating studies utilize upward solidification techniques where the solid ice is in contact with a cold-plate and proceeds vertically upward, against gravity. Liquid water reaches its maximum density at 4 °C; thus, liquid nearest the solid/liquid interface is less dense than the warmer liquid above (assuming all water above is below 4 °C), so the liquid at the solid/liquid interface is unstable with respect to buoyancy; this <4°C water is expected to rise, promoting convective fluid motion in the liquid region during solidification. We investigated the effect of solidification direction (Fig. 3) with respect to the direction of gravity on ice-templated microstructures to study the role of buoyancy-driven fluid motion during solidification. We hypothesized that, for upward solidification, the convective fluid motion that results from the liquid density gradient would occur near the solidification front. For downward solidification, we expected that this fluid motion would occur farther away from the solidification front. Aqueous suspensions of TiO2 nanoparticles (10-30 nm in size, 10, 15, and 21 vol.%) were solidified upward (against gravity, with ice on bottom and water on top), downward (water on bottom, ice on top), and horizontally (perpendicular to gravity). Microstructural investigation of sintered samples showed evidence of buoyancy-driven, convective fluid flow during solidification for samples solidified upwards (against gravity), including (i) tilting of the wall (and pore) orientation with respect to the induced temperature gradient, (ii) ice lens defects (cracks oriented perpendicular to the freezing direction), and (iii) radial macrosegregation (Fig. 4). These features are not observed for downward nor horizontal solidification configurations (Fig. 5), which was consistent with our hypothesis that convective fluid motion does not interact directly with the solidification front for downward solidification of our water/TiO2 suspensions.
Effect of Initial Suspension Temperature
Pierce Pettit and Kristen Scotti
Ice-templating of suspensions that are held at room temperature prior to solidification will exhibit a double-density gradient during solidification because of water's density extremum at 4 °C. Liquid water reaches its maximum density at 4 °C; thus, for the upward solidification configuration (solid ice on bottom, liquid suspension on top, Fig. 3), the liquid nearest the solid/liquid interface will be close to the melting point of ice (0 °C) and less dense than the water immediately above the water at the interface. The density of the water will continue to decrease with distance away from the interface up to the 4 °C isotherm. The water above the 4 °C isotherm, still above the water at the interface, will be more dense than the water below that line due to the density inversion of water at 4 °C. This inversion in density gradient in the fluid during solidification is expected to result in complex, buyancy-driven fluid patterns during solidification. To investigate the microstructural effects of the density inversion of water at 4 °C, we are solidifying aqueous TiO2 suspensions at varying initial suspension temperatures and comparing resulting microstructures.

Fig. 1. Freeze-casting process. A suspension consisting of particles (grey) dispersed in a fluid (dark blue) is (a) placed onto a freezing substrate; (b) solid dendrites (light blue) propagate in the direction of the thermal gradient while pushing particles away from the moving front. An accumulation region (c) of rejected particles develops ahead of the solid/liquid interface, inducing particle packing within interdendritic space. After (d) complete solidification, the solidified fluid is (e) removed via sublimation leaving elongated pores (white) which template the dendrites. The remaining particle scaffold is (f) sintered to densify particle-packed walls (black).
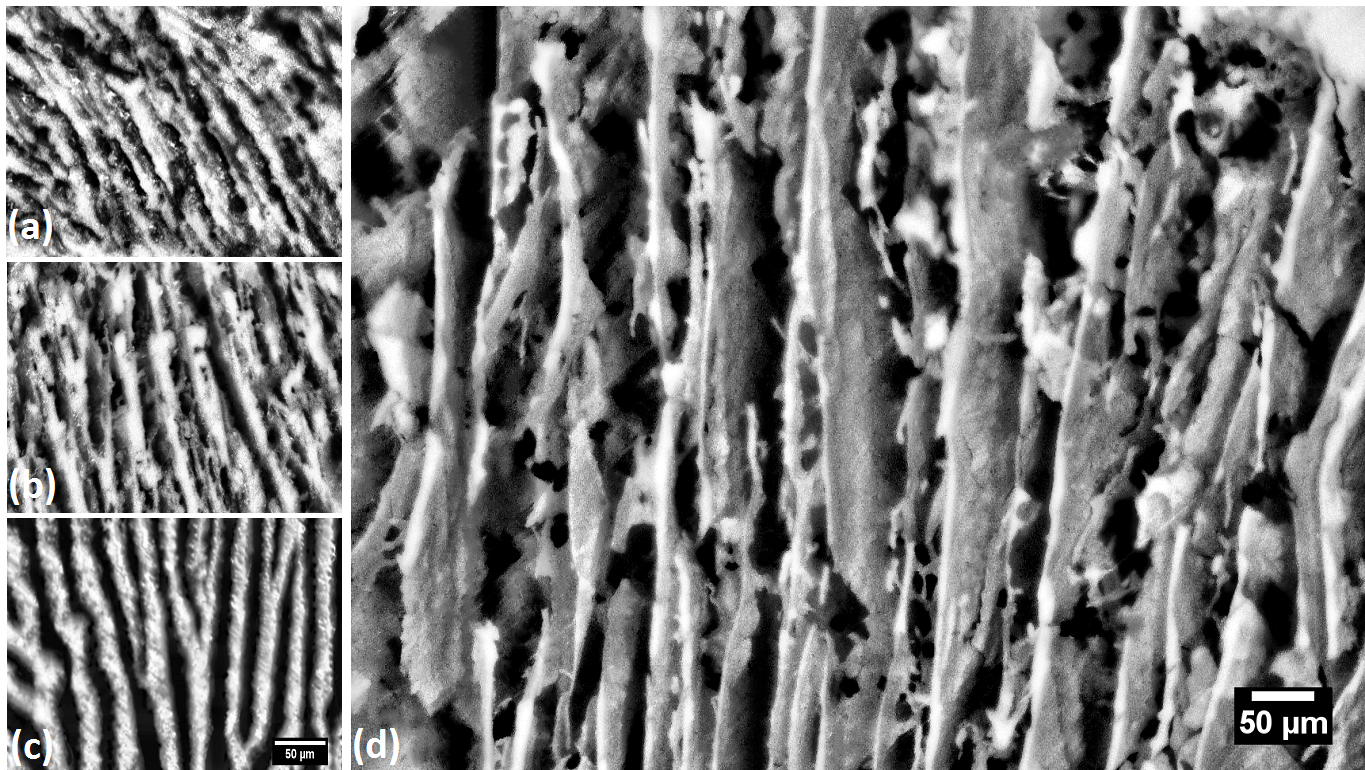
Fig. 2. Longitudinal cross sections of ice templated TiO2 (20 wt.%) solidified under (a) terrestrial, (b) martian, (c) lunar, and (d) microgravity on parabolic flights (g = 10-6, 1.62, 3.71, and 9.81 m/s2, respectively).
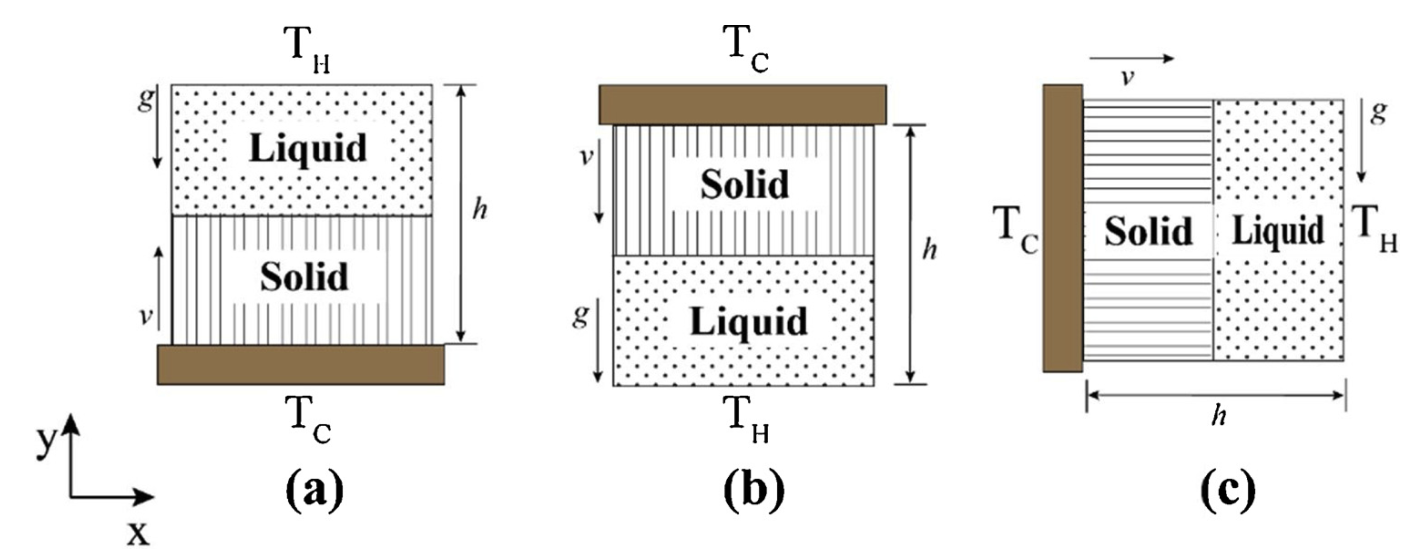
Fig. 3. Diagram showing the experimental set-up for (a) "Up", (b) "Down", and (c) "Horizontal," solidification conditions where TH and TC represent the hot and cold side of the mold, respectively, and h is the mold height which is filled completely with the TiO2 aqueous suspension. The solidification direction (v) is (a) upward, (b) downward, and (c) horizontal, with respect to the direction of gravity (g)
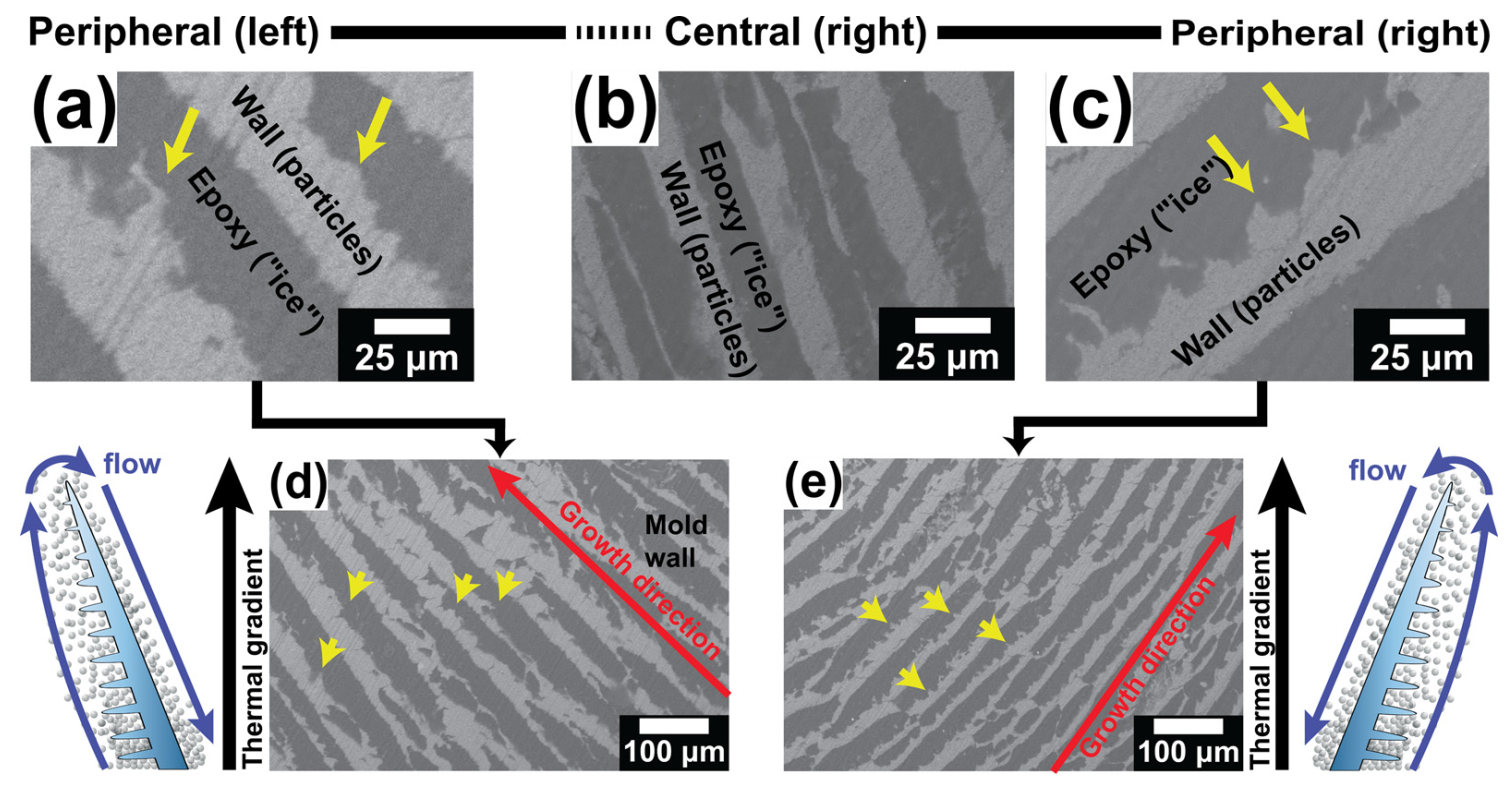
Fig. 4. SEM micrographs of polished longitudinal cross-sections of sintered, freeze-cast TiO2 obtained by solidifying aqueous suspensions containing 30 wt.% TiO2 nanoparticles vertically upward. Images in the top row are obtained from the: (a) left-peripheral (near mold wall), (b) central-right, and (c) right-peripheral (near mold wall) regions of the sample; (d) and (e) are lower magnification images of (a) and (c) respectively. Asymmetric secondary dendritic arms (yellow arrows) are observed in (a, d) and (c, e) where the ice growth direction diverges significantly from the direction of the imposed thermal gradient; these features are minimized in (b) where the tilt angle (θ; ice growth direction) is minimized
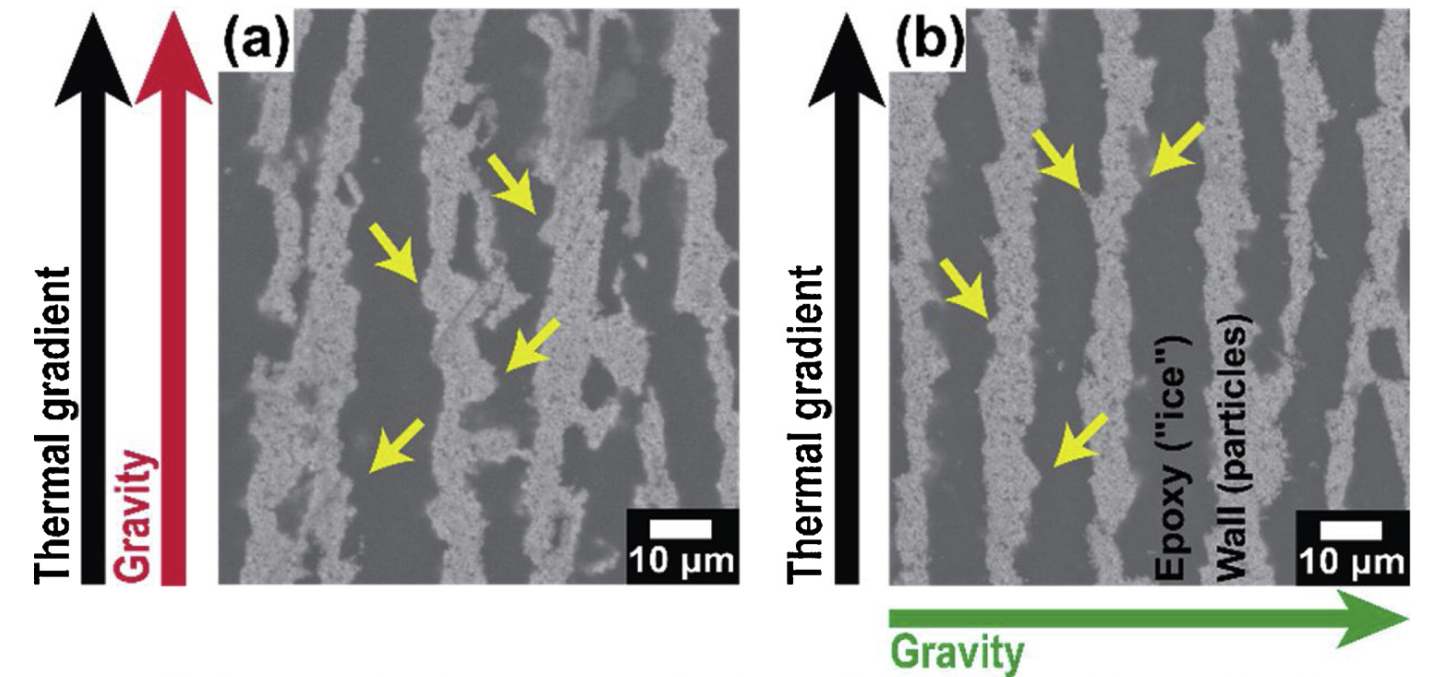
Fig. 5. SEM micrographs of polished longitudinal cross-sections of sintered, freeze-cast TiO2 obtained by solidifying aqueous suspensions containing 30 wt.% TiO2 nanoparticles (a) vertically downward and (b) horizontally with respect to gravity. Secondary dendritic arms (yellow arrows) are observed on both sides of lamellae for both downward and horizontal solidificaiton configurations.
Related Publications
- Scotti, K.L. & Dunand, D.C. (2017). Freeze Casting: A review of processing, microstructure and properties via the open data repository, FreezeCasting.net. Submitted to: Progress in Materials Science.
- Scotti, K.L., Northard, E.E., Plunk, A., Tappan, B.C., & Dunand, D.C. (2017). Directional solidification of aqueous TiO2 suspensions under reduced gravity. Acta Materialia, 124, 608-619.
- Scotti, K. L., Kearney, L. G., Burns, J., Ocana, M., Duros, L., Shelhamer, A., & Dunand, D. C. (2019). The effect of solidification direction with respect to gravity on ice-templated TiO2 microstructures. Journal of the European Ceramic Society, 39(10), 3180-3193.
Funding support
- NASA Flight Opportunities Program
- NASA Office of Education
- Illinois Space Grant Consortium
- Institute of Sustainability and Engergy at Northwestern
- Northwestern University Office of the Provost